FLUID MECHANICS LABORATORY
LAB IN-CHARGE
Mr. KOROUNGAMBA LAISHRAM
B.Tech, M.Tech, Pursuing PhD
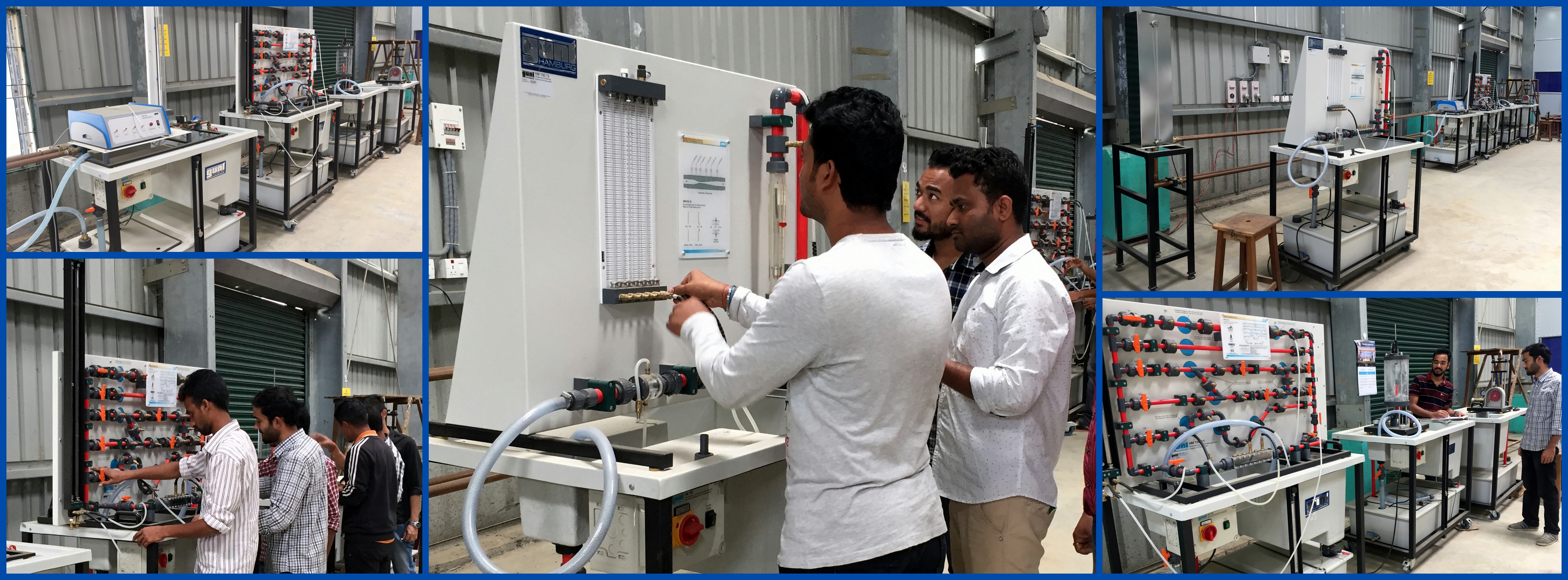
The Fluid Mechanics Laboratory was established in June 2016 with the core objective of imparting hands-on pragmatic knowledge in the field of water technology and allied research with respect to the theoretical courses taught to the graduate, post-graduate and PhD students of civil engineering. It houses state of the art advanced instrumentation and latest assembly of equipments supplied by Gunt, Hamburg, Germany and other manufacturers. The laboratory is located in the departmental workshop building of the institute with a floor area covering 600 sq.m.Â
Fluids (generally liquids) are transported from one location to another using natural or constructed conveyance structures. The cross section of these structures may be open or closed at the top. The structures with closed tops are referred to as closed conduits and those with the top open are called open channels. For example, tunnels and pipes are closed conduits whereas rivers, streams, estuaries etc. are open channels. The understanding of motion and behaviour of fluids under varied conditions and boundaries, demands a lucid practical knowledge of the subject apart from the class room courses comprising of mathematical expressions and formulae. The validation of these basic principles of the subject is conducted in the laboratory. The laboratory recognizes evolution in the application of fluid mechanics and hydraulic engineering, as well as the necessity to reinforce and underpin the student’s understanding of its fundamental precepts and actual field applications.Â
As in basic inception of any laboratory or practical study room, the Fluid Mechanics Laboratory will emphasize the linkage between theory and practice. The laboratory exercises provided with well-illustrated manuals and guided by respective faculties and technical assistants, fall into a number of natural categories, firstly relatively simple calculations, for example friction factor ; then calculations designed to provide solutions for steady state system operation as turbine or pump operating systems, water hammer and surges in response to changes in fluid system operating conditions
List of Equipments
- Base module for experiments in Fluid Mechanics
- Methods of Flow measurement
- Losses in a Piping system
- Stability of Floating Bodies
- Hydrostatic Pressure Apparatus
- Measurement of Jet Forces
- Bernoulli’s Principal Demonstrator
- Flow Over weir accessories
- Osborne Reynolds experiment
- Operating principal of a Pelton Turbine
- Speed Sensor
- Operating principal of a Francis Turbine
- Experiment with a Centrifugal Pump
List of Experiments:
- Demonstration set for Bernoulli’s Theorem
- Discharge through a Nozzle
- Coefficient of Discharge of an Orifice Meter, Venturimeter, etc
- Pitot Tube and Coefficient of Velocity
- Hydraulic Ram Pump and its Efficiency
- Friction Factor and Losses in Pipes (Combination, Separation, Sudden Contraction and Enlargement)
- Water Hammer Chamber and Surge Chamber demonstration set with Automated Plotting unit
- Pelton Wheel Turbine – Power Output and Efficiency
- Francis Turbine – Power Output and Efficiency
- Jet Apparatus for Impact Forces
- Centrifugal Pump - Efficiency
- Stability of Floating Body
- Reynold Osborne Experiment
HM 150.11- LOSSES IN A PIPE SYSTEM
HM 150.13 METHODS OF FLOW MEASUREMENT (VENTURIMETER, ORIFICEMETER, NOZZLE, PITOT TUBE)
HM 150.06 STABILITY OF FLOATING BODIES
HM 150.07 BERNOULLIS PRINCIPLE
HM 150.08 MEASUREMENT OF JET FORCES
HM 150.16 SERIES AND PARALLEL CONFIGURATION OF PUMP
HM 150.18 OSBORNE REYNOLDS EXPERIMENT
HM 150.19 OPERATING PRINCIPLE OPF PELTON TURBINE
HM 150.20 OPERATING PRINCIPLE OF A FRANCIS TURBINE
HM 150 BASE MODULE FOR EXPERIMENTS
HM 150 EXPERIMENT FOR NOTCHES
HM 150.05 HYDROSTATIC PRESSURE IN LIQUIDS